In the pharmaceutical industry, maintaining strict air quality, temperature, and humidity levels is critical to ensuring product safety and regulatory compliance. Air Handling Units (AHUs) play a vital role in achieving these standards by providing clean, controlled, and contaminant-free air.
With increasing regulatory scrutiny and the rising demand for high-purity drug production, pharmaceutical companies must invest in high-performance AHUs to protect both product integrity and patient health. In this article, we explore why AHUs are indispensable in pharma facilities and how they help maintain compliance with international standards.
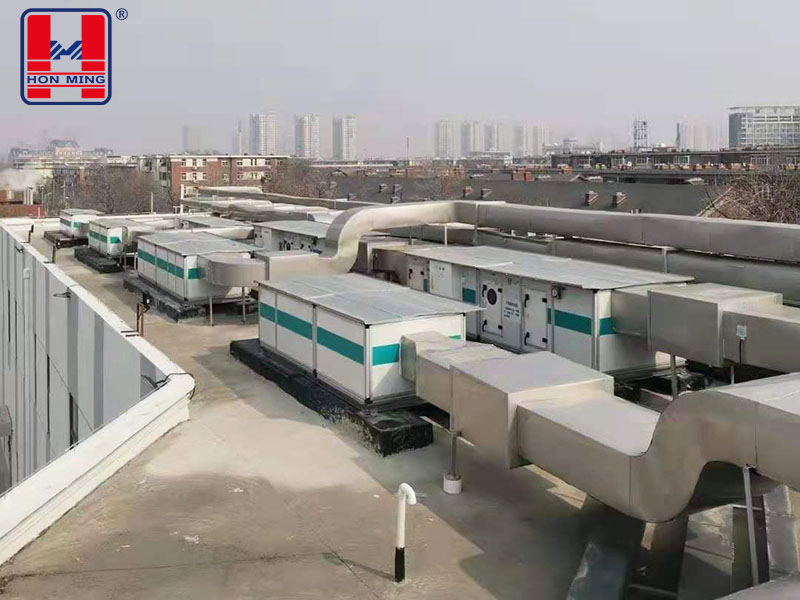
1. The Critical Role of AHUs in Pharmaceutical Facilities
An AHU (Air Handling Unit) is the heart of an HVAC system, responsible for:
✔ Filtering and purifying air to eliminate airborne contaminants.
✔ Regulating temperature and humidity to ensure drug stability.
✔ Maintaining positive or negative pressure in cleanrooms to prevent cross-contamination.
✔ Ensuring compliance with cGMP, FDA, and WHO guidelines for pharmaceutical manufacturing.
Without an efficient AHU system, pharmaceutical production can be at risk of contamination, regulatory non-compliance, and compromised product quality.
2. Key Features of Pharmaceutical AHUs
To meet the strict environmental requirements of drug manufacturing, pharmaceutical AHUs are designed with advanced features:
Multi-Stage Filtration System
- HEPA & ULPA filters remove airborne particles as small as 0.3 microns.
- Pre-filters & activated carbon filters trap dust, bacteria, and chemical contaminants.
Temperature & Humidity Control
- Ensures consistent environmental conditions for drug formulation, preventing degradation.
- Essential for biotechnology, vaccine production, and sterile environments.
Airflow & Pressure Management
- Positive pressure prevents outside contaminants from entering sterile areas.
- Negative pressure ensures hazardous substances remain confined in specific zones.
Energy-Efficient Design
- Variable Frequency Drives (VFDs) optimize airflow, reducing energy costs.
- Heat recovery systems improve efficiency and sustainability.
3. Compliance & Regulatory Requirements for AHUs in Pharma
Pharmaceutical AHUs must meet strict regulatory guidelines to ensure GMP-compliant cleanroom operations. Some key standards include:
FDA (Food & Drug Administration) Regulations – Ensures air purity in drug manufacturing facilities.
cGMP (Current Good Manufacturing Practices) – Requires precise control of air handling and filtration.
ISO 14644 Cleanroom Standards – Defines air cleanliness levels and particle control.
WHO Guidelines for Pharmaceutical Cleanrooms – Regulates airflow, pressure differentials, and air quality.
Failure to comply with these regulations can result in product recalls, facility shutdowns, and legal penalties.
4. Why Upgrading Your AHU System Is a Smart Investment
Investing in a state-of-the-art pharmaceutical AHU offers multiple benefits:
✔ Higher product safety – Eliminates airborne contamination risks.
✔ Regulatory compliance – Meets international cleanroom air quality standards.
✔ Energy efficiency – Reduces operational costs with smart airflow management.
✔ Better workplace safety – Protects employees from exposure to hazardous substances.
5. Conclusion: The Future of Air Handling in Pharma
With the rise of biopharmaceuticals, gene therapies, and precision medicine, pharmaceutical manufacturers need advanced AHU solutions to meet evolving industry demands.
An efficient, GMP-compliant AHU is no longer optional—it’s a necessity for ensuring drug safety, regulatory compliance, and operational efficiency.
Are you looking for high-performance AHUs for your pharmaceutical facilityContact us today for expert solutions! ?